Hello again guys, a few more images for you of on-going work on the Bedford.

So, with the rear axle and springs in position it was time to fasten them onto the chassis.

Front first up and making a start on a few shapes trying to get the placement judged:
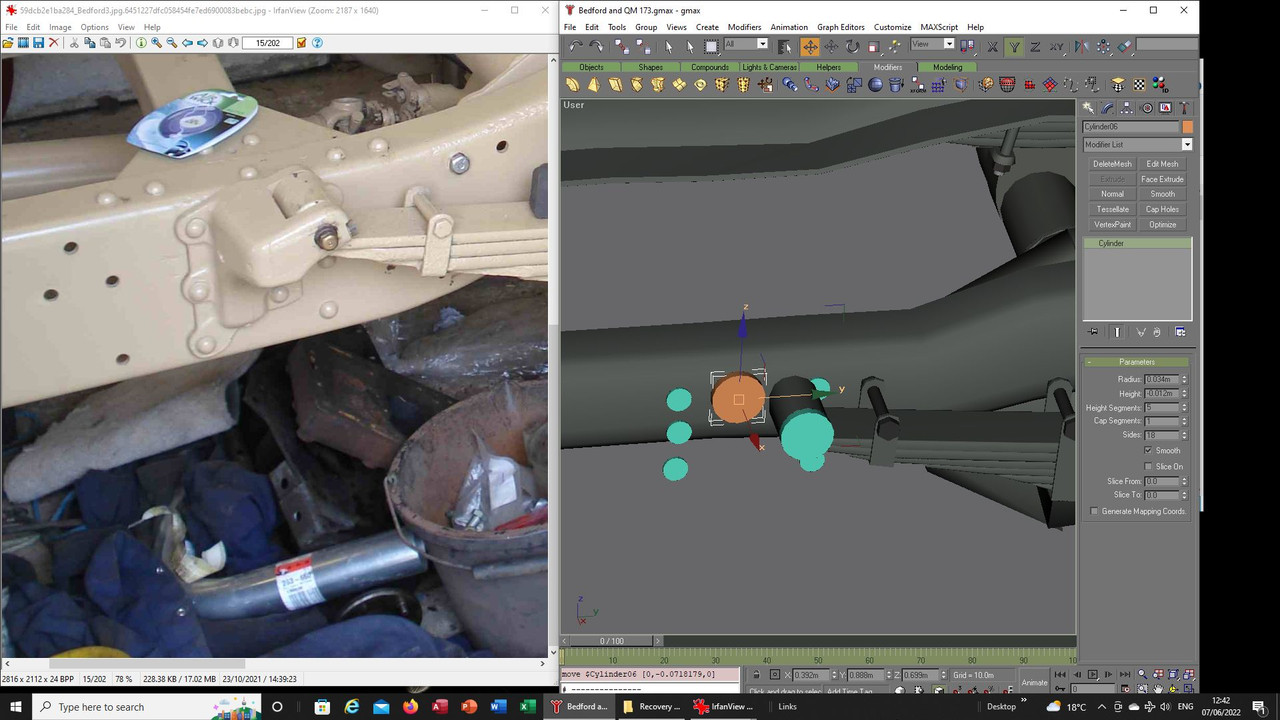
Trying to replicate the shape of things is always a little hit and miss, I just start making a few few shapes
and see where it takes me:
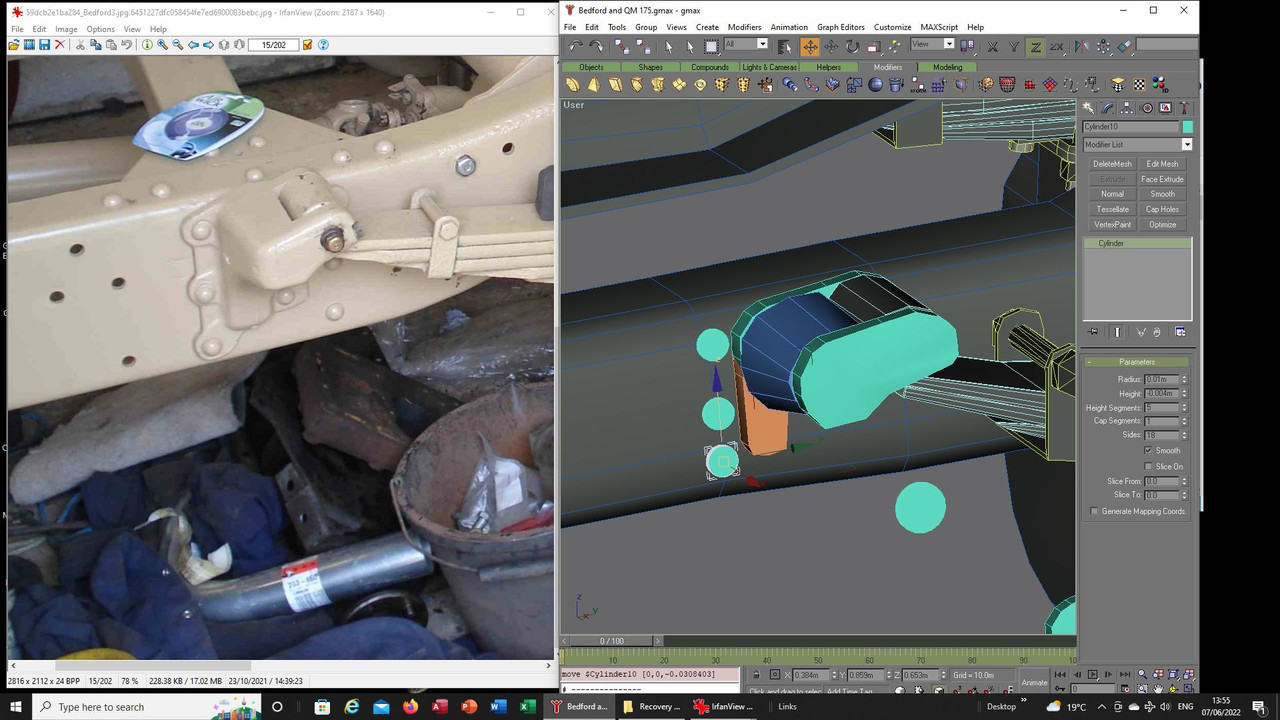
This is what it became, later things will be attached and welded but at least I now settled on the shape of
and placement of things:
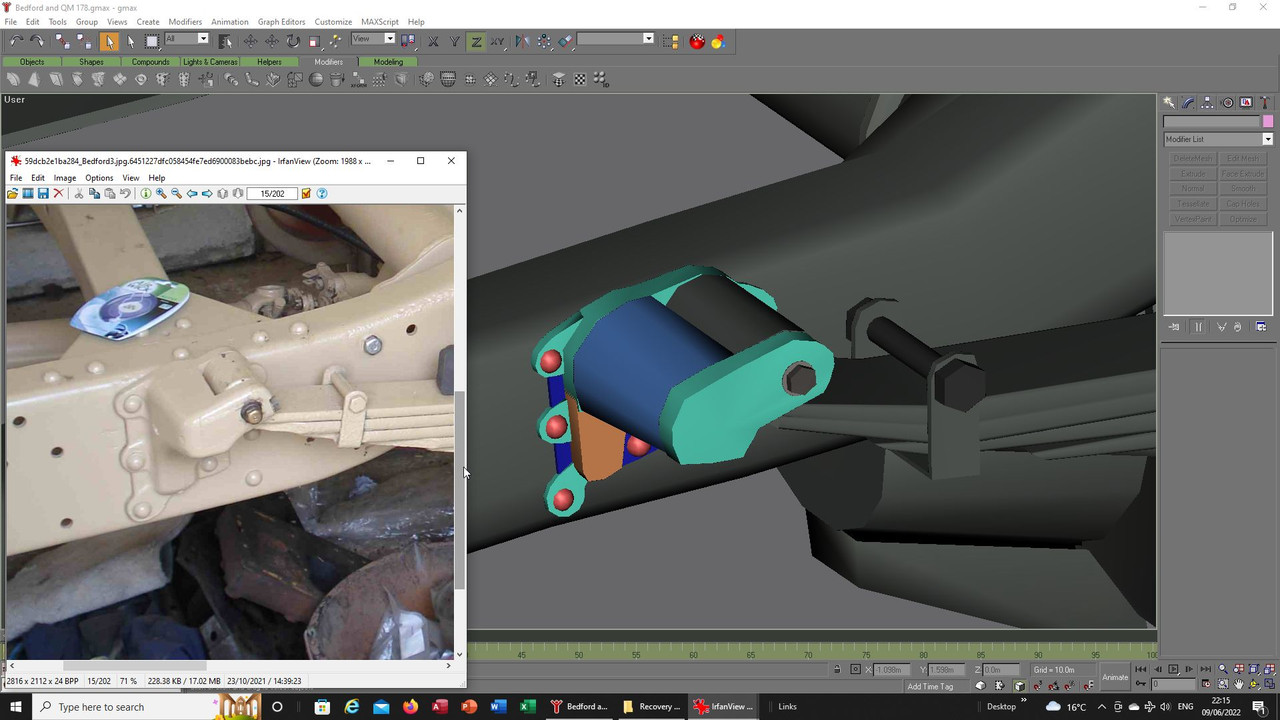
Here welding has begun, any faces not required in the finished shape have been deleted so this becomes
the final component:
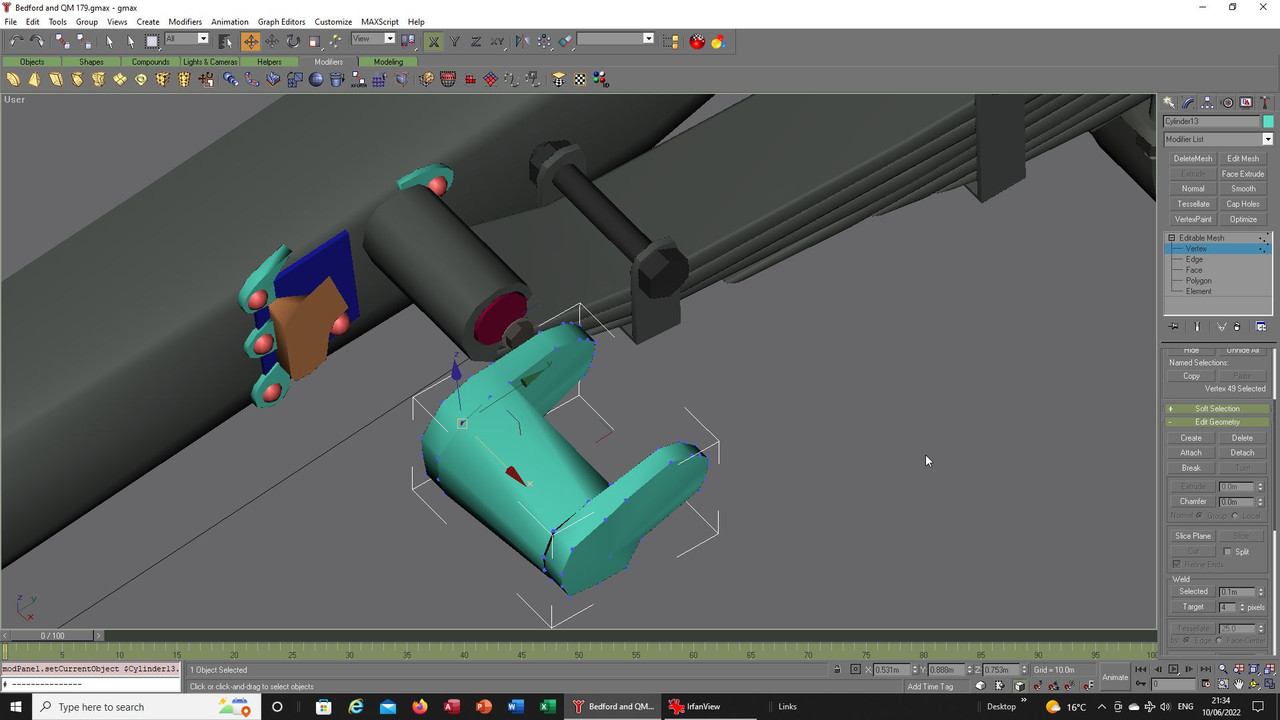
Most of the mapping is done and a few extra parts now get some attention to complete things as best I can
per the images:
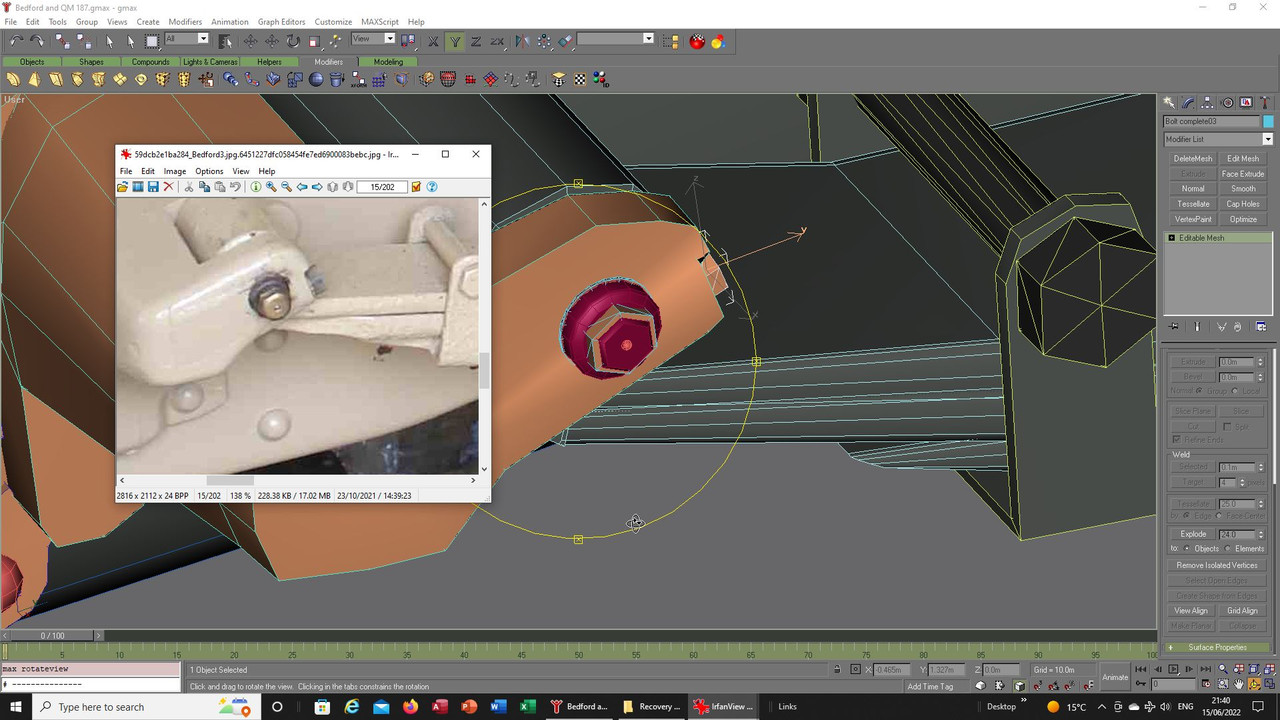
Front fixings done and in position, they have also been cloned and adjusted for the other side:
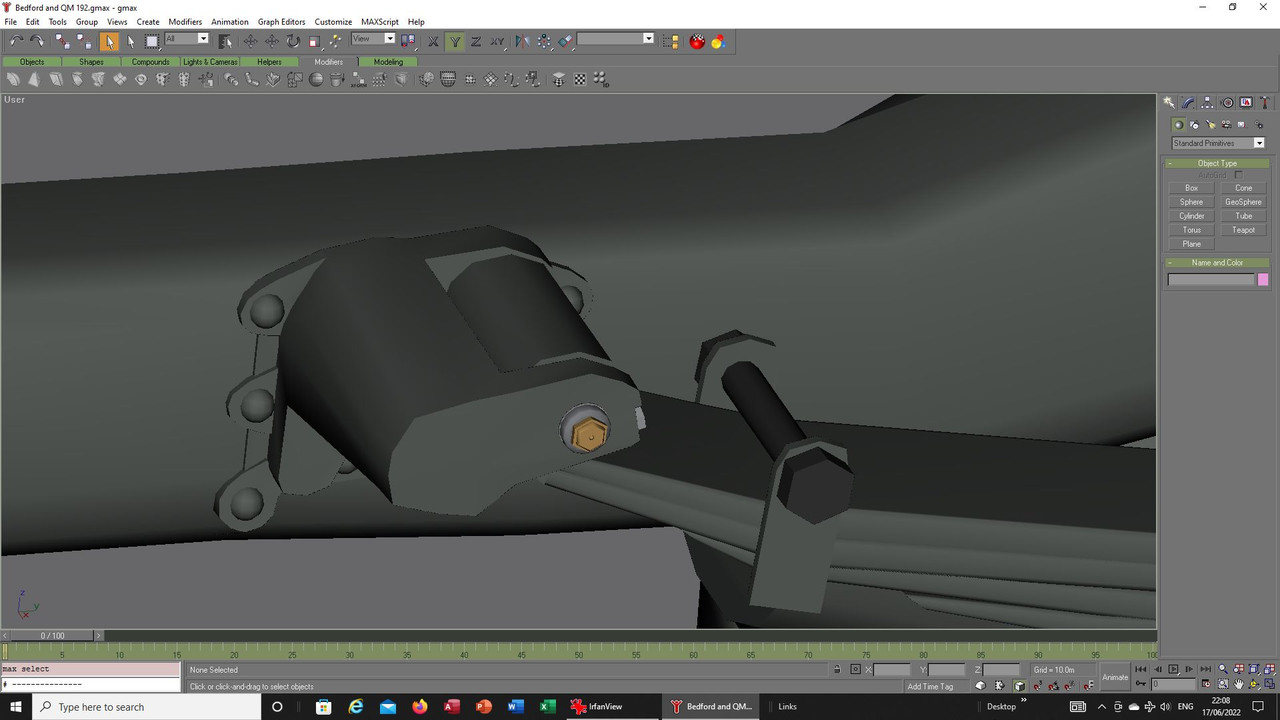
The rear fixing starts its progress, this is a casting and as you can see is a rather complex shape so I
have made a start on that with the line tool:
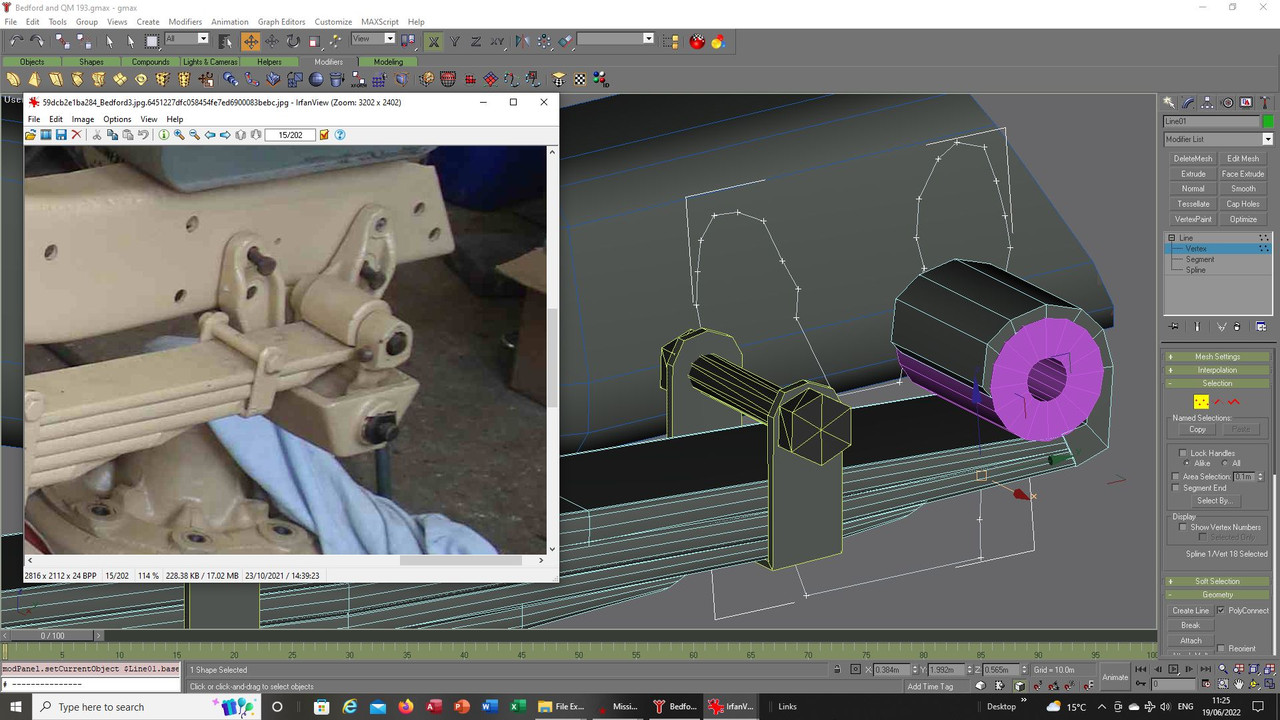
I made two shapes, one for the back and the other to try and replicate the sides:
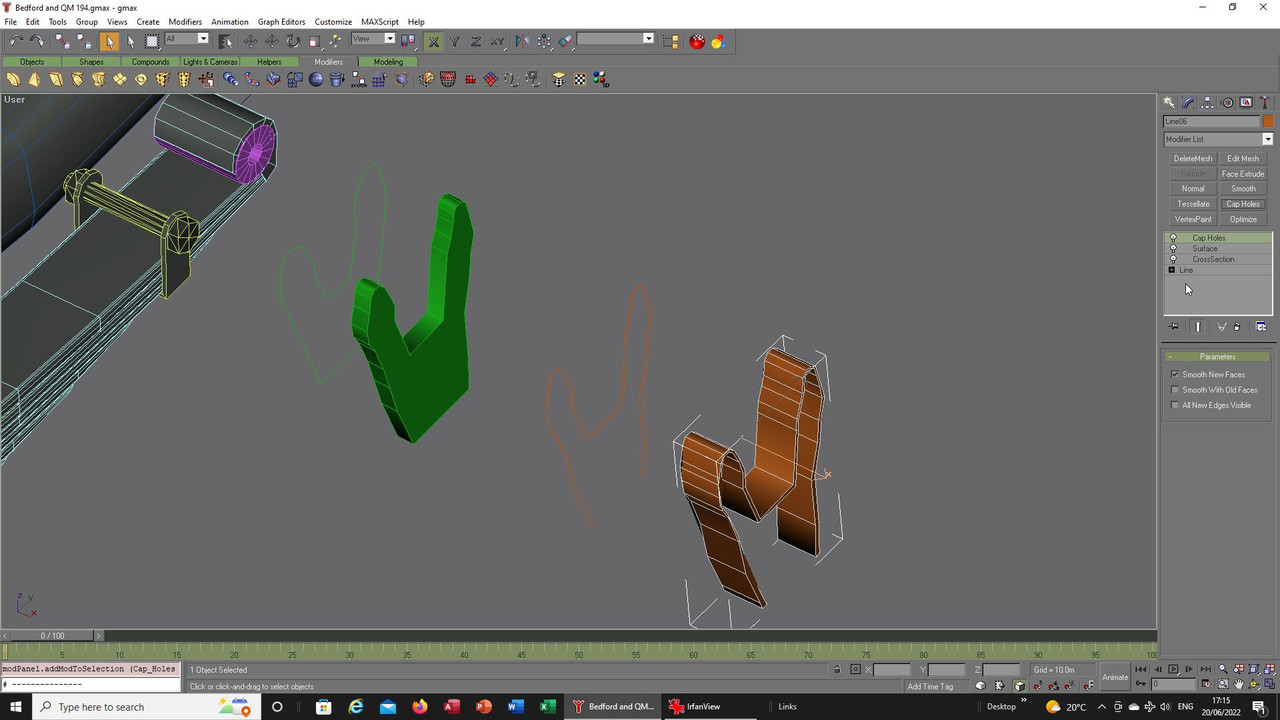
The idea is to cut these up and eventually weld together what is left, the front inner green face will need to
be separated and shrunk slightly and ultimately welded to the sides:
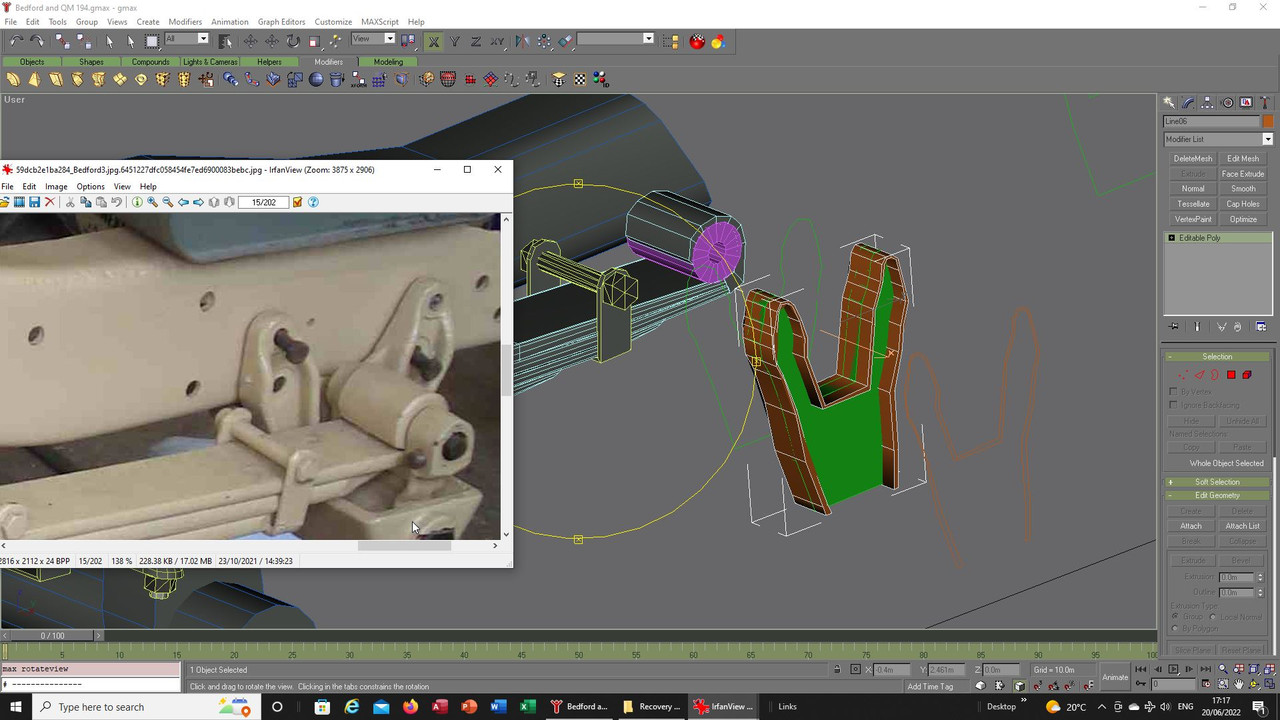
This is from the rear, the faces that join front and rear faces of the green piece are removed and the front
will be re-sized, the arms have had some shaping done at the top:
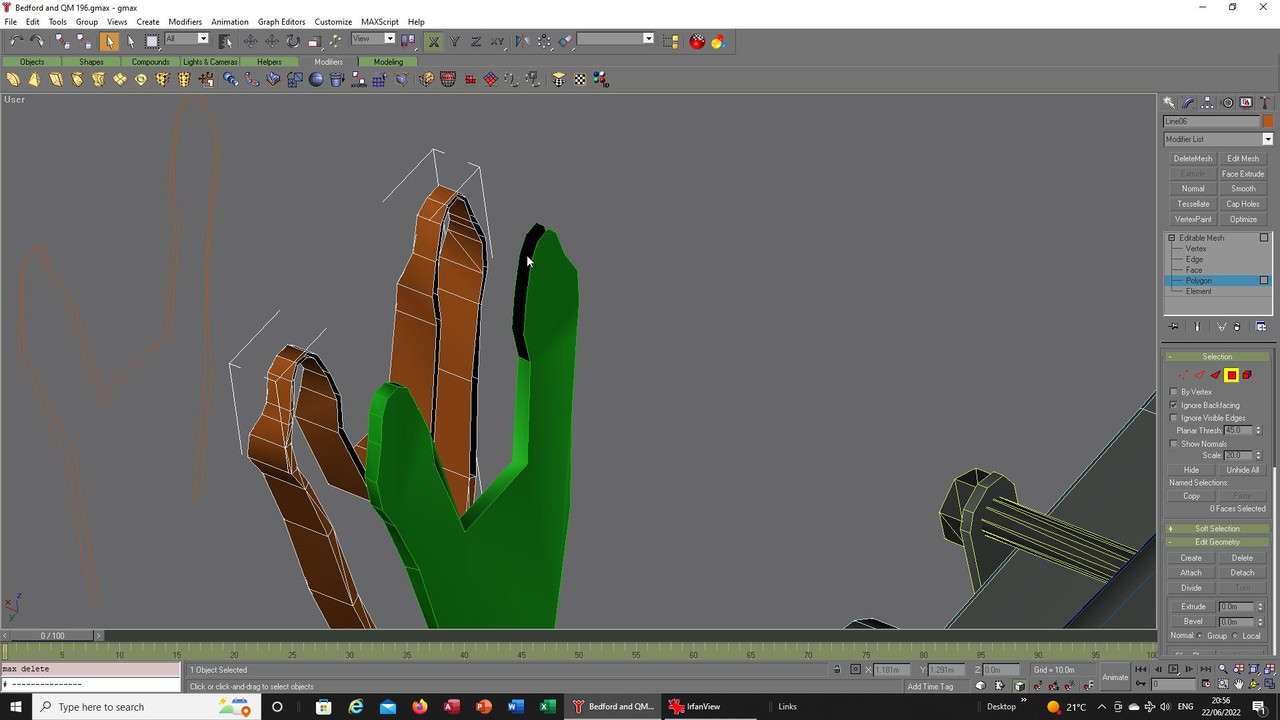
Here you see the inner face of the arms having been pushed further forward being welded to what will be the
front face of the casting, this will leave a gap and then the rear face will be welded to the outer vertices:
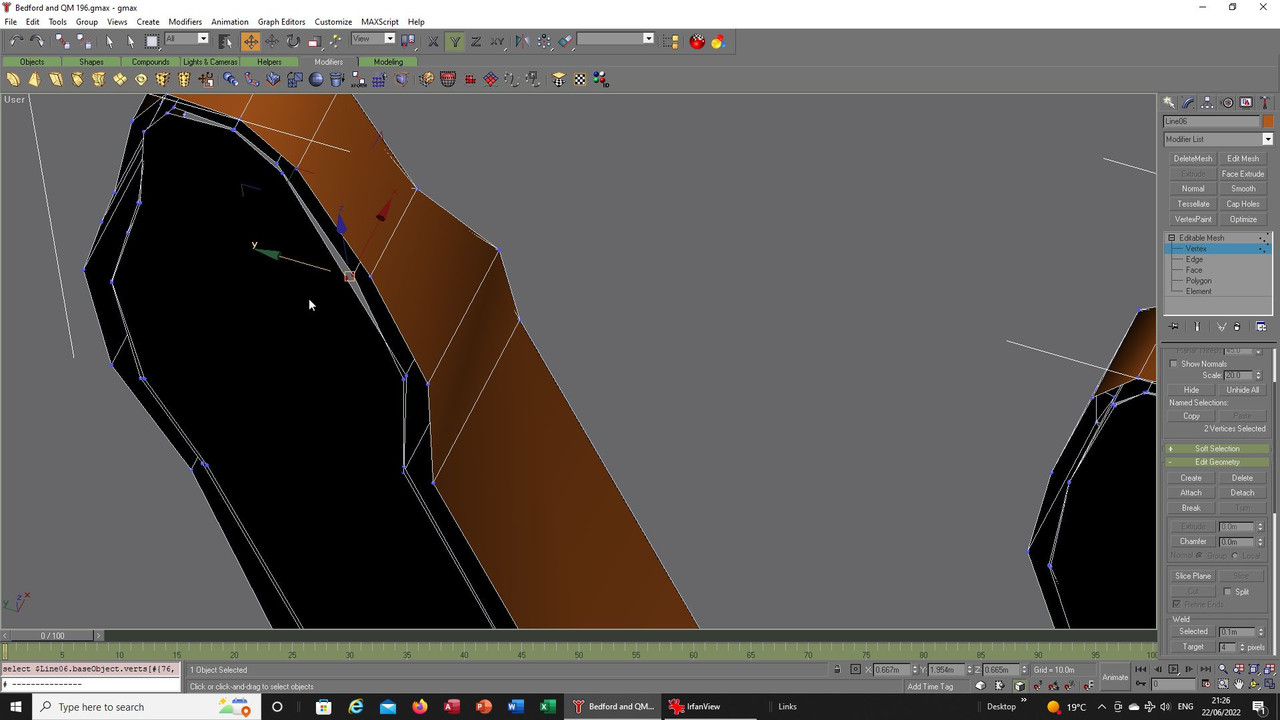
Here the back is added, I do not have a full idea of how these shapes will be constructed when I begin, a vague
idea takes shape but usually as the real world intervenes a lot of tinkering follows before it finally comes together.
I could have made a solid and plunged another shape into that using the Boolean tool but it sometimes gets messy
that way so this way was what I settled on eventually:
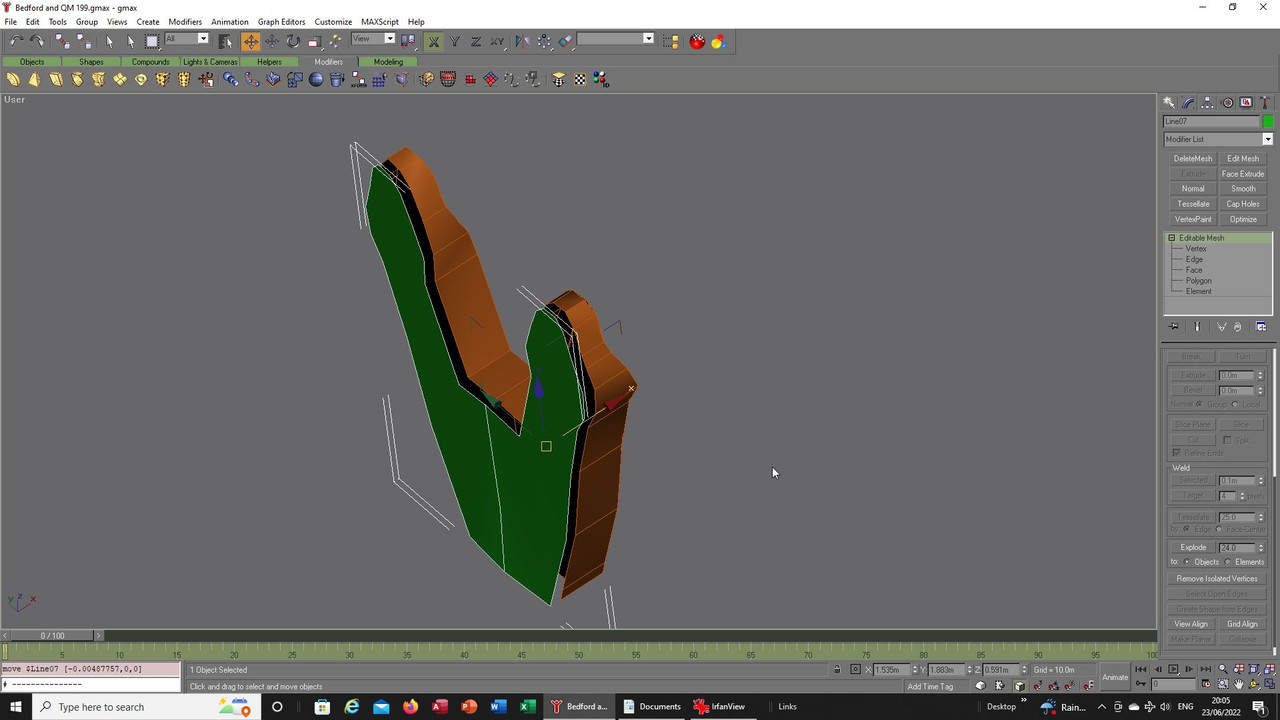
Filling in the rest of the overall fixture:
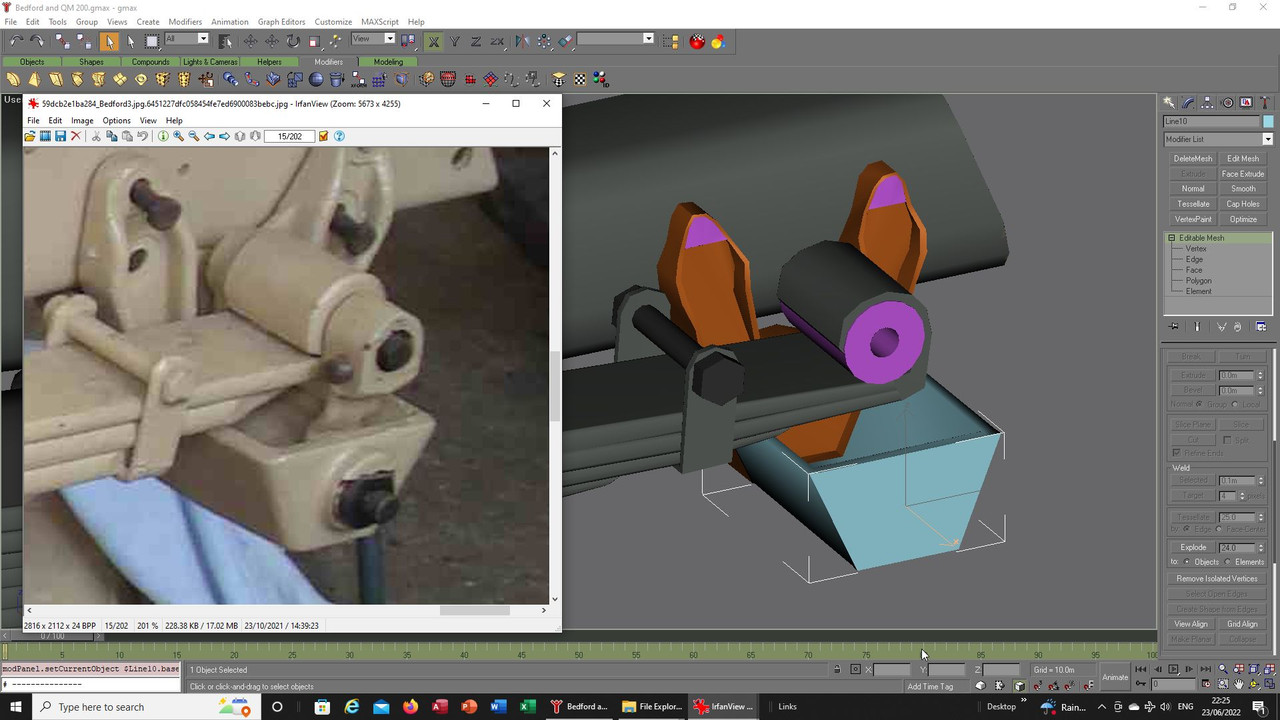
And eventually we get to where I want to be, construction done and mapping ready to begin:
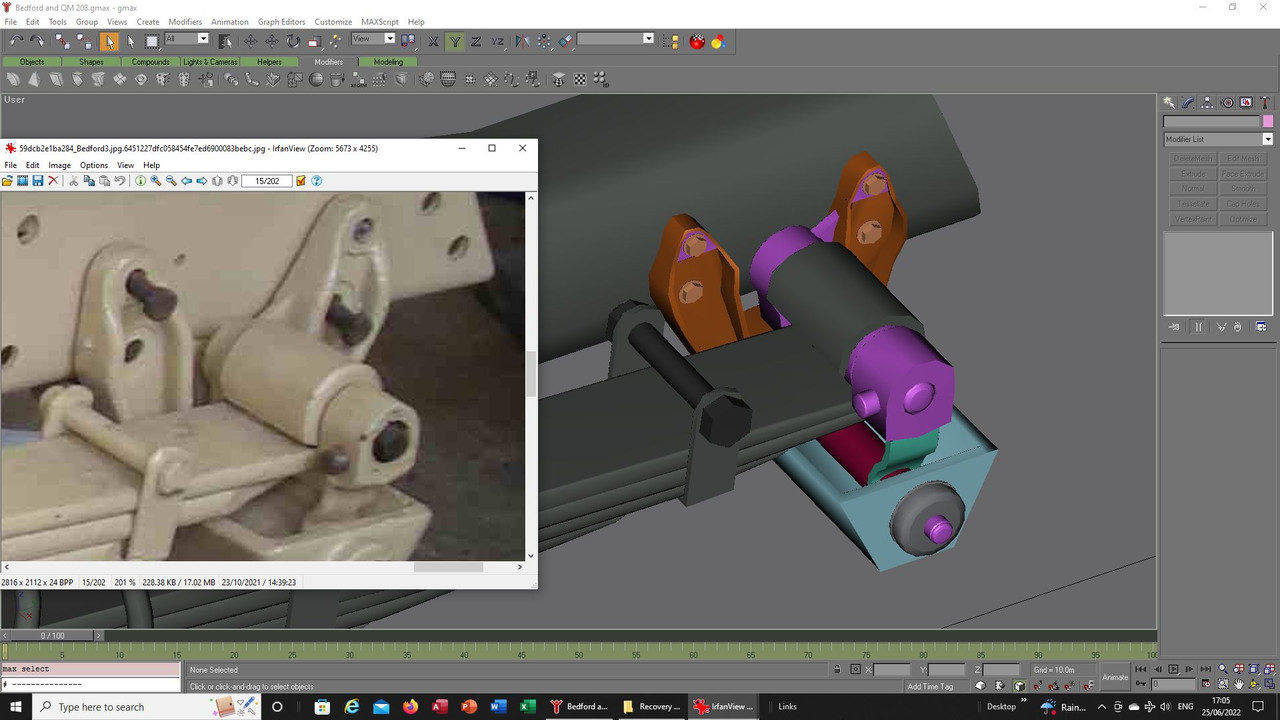
Next time you see this the paint should be on and I can then look at other areas of the model.

Take care and be safe.
Wishing you all the very best, Pete.
